Crystalline waterproofing materials remain a terrific way to protect your basement walls from the damage that water does by penetrating and freezing in your foundation.
In this process, crystalline waterproofing material is brushed onto basement walls. Here it penetrates the concrete cavities and forms a strong bond. This changes the porous concrete into a waterproof solid.
This process is most effective in a wet basement where water seepage is a problem.
One significant advantage of this material is that installation is straightforward and can be accomplished by any do-it-yourself homeowner.
Step 1: Cleaning
Before you begin application, you must completely clean the concrete wall surfaces. The crystalline waterproofing material will only adhere to the concrete surface if it is free from any other debris or dust. Use a wire brush to remove loose concrete or paint. A hammer and chisel may be needed for large pieces of concrete that are loose but can’t be brushed off. If there are multiple layers of paint that cover a wide area, you could try power washing the surface or even sandblasting it.
Step 2: Preparing
The next step is to repair your concrete surface by filling large cracks. Using concrete patch or liquid concrete in a tube, spread it over the surface with a trowel. Fill the crack completely and let it dry and set before doing anything else to the surface.
Step 3: Priming
Next you will prime the concrete for the crystalline waterproofing by thoroughly wetting the surface of the concrete with water. You don’t want to soak the area, but it should be damp, which will actually help with spreading and adhering the waterproofing substance.
Step 4: Mixing
In a bucket, you should mix the crystalline waterproofing material with water, according to the instructions. Apply just enough water so that the material becomes a thick paste.
The chemical process of the water and the material will cause the substance to warm. This is a natural and expected process, and evidence you are doing it correctly.
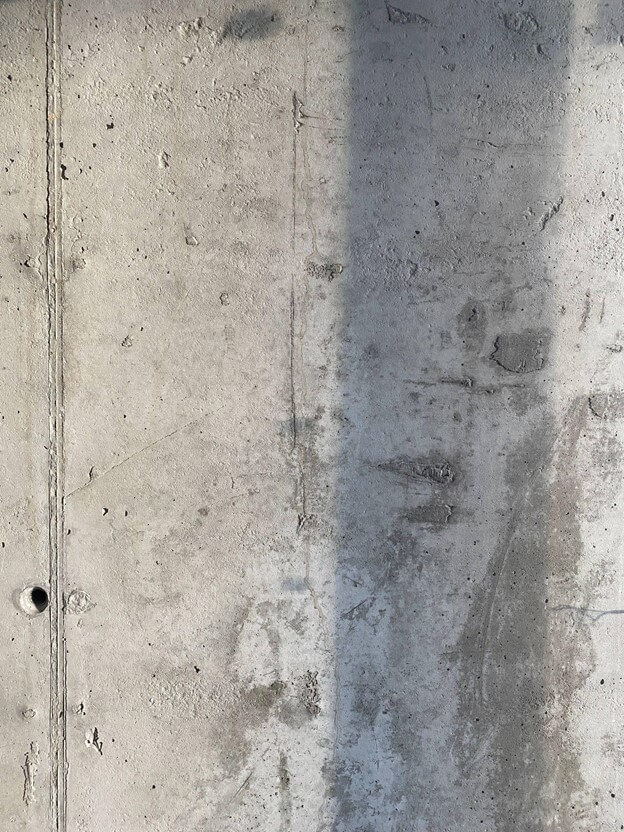
Photo by Yuriy Pavlov on Unsplash
Step 5: Applying
Using a masonry brush, apply a thick coating of the paste to the concrete wall. Make this coat thick but even.
Step 6: Curing
Once the crystalline waterproofing material is applied to the surface of the concrete, you must keep it wet for at least 48 hours. Lightly spray it with a misting bottle. This allows the materials to penetrate into porous concrete. If it sets too quickly, it won’t combine correctly and you will have wasted your time.