When contractors are waterproofing commercial, or industrial spaces, they often rely on sheet membranes to offer the best possible protection against water. In concrete waterproofing, sheet membranes are applied to either external surfaces. Together the concrete and membrane form a nearly impenetrable barrier.
Despite the double barrier, waterproofing membranes can still fail. Here are some common reasons why.
A failure of skilled application
The application of waterproofing sheet membranes is a very labor intensive task. The workers who apply it need training and experience to do the job well under the best circumstances. However, because it is so dependent on labor, this is where the failures occur. Some estimates suggest that poor workmanship alone accounts for 90% of all waterproofing membrane failures.
Debonding can be caused by several factors, including application to an uneven surface or to a wet surface. Application to contaminated surface, lack of primer, or insufficient priming of the surface prior to installation of the waterproofing sheet membrane can lead to debonding.
Further, insufficient coverage or uneven application of a membrane prevents establishing a uniform thickness of the waterproofing layer. This can result in the failure of the application as thinner parts of the membrane get damaged quicker, not fully bonding overlaps pose potential breach of the waterproofing layer. Membranes can then come apart at the seams and allow water to penetrate.
Companies can overcome this with training, experience, and teamwork. Everyone needs to do this the first time, so experience alone isn’t the answer. But careful oversight can prevent catastrophe.
Choosing the wrong components
Choosing the wrong membrane, using the wrong items for the intended application, or matching the membrane with the wrong substrate can lead to the failure of the waterproofing application.
In matching the selected membrane with primers, it is important to select complementary products. Failure to do so can lead to an unbonding of the membrane and failure of the waterproofing. Unbonding is when the sheet membrane no longer forms a watertight seal with the concrete, allows water migration between the membrane layer and the concrete.
To mitigate this problem, sheet membranes for underground waterproofing applications must meet international standards. Choosing from EPDM, TPO, or PVC membrane types is important, but selecting the right primers allows the sheet membrane to be fully mechanically adhered to the substrate, however these might not be the right combination for below grade applications.
Another common problem is blister. Blister is caused by insufficient prime at the surface. As a result, trapped air builds up under the membrane causing debonding and blistering. These blisters are prone to puncture and then result in a breach of the waterproofing layer allowing water to pass through to the concrete. Waterproofing sheet membranes are exposed to a high risk of damage.
Often this damage occurs in the subsequent stages of the construction schedule. Both puncturing and tearing represent a breach of the waterproofing layer and thoughts of failure.
The effects of time
Many waterproofing membranes deteriorate over time, due to exposure to UV rays, harsh environments, aggressive groundwater, or permanent ponding leading to the disintegration of the waterproofing layer. Ultimately this leads to the failure of the membrane.
In conclusion, membranes are not recommended for certain types of projects. Efficient and long lasting waterproofing solutions require newer technologies that permanently reduce permeability and improve concrete properties and durability.
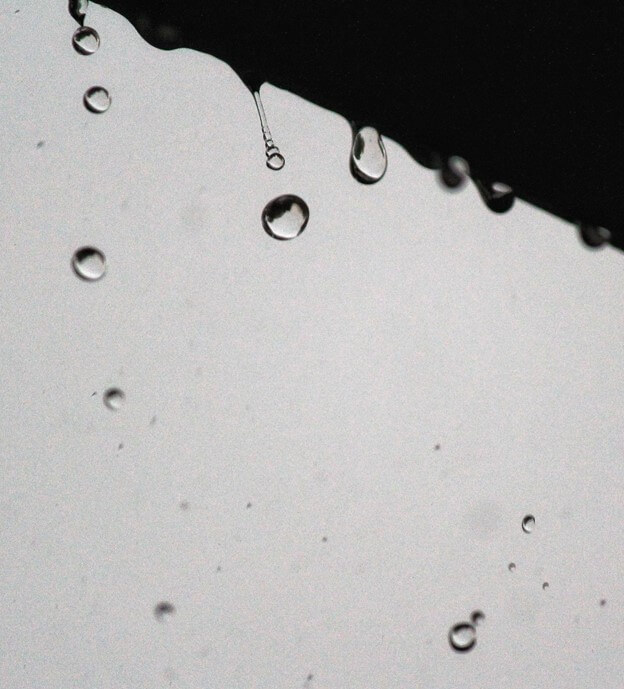
Photo by Holly Obermiller on Unsplash